Ernst KNOLL Feinmechanik GmbH
Tradition, precision and responsibility
Established as a family business over 60 years ago, KNOLL Feinmechanik is a recognised specialist for automation solutions in the manufacturing of medical articles as well as for industrial assembly processes where the highest precision is required.
Environmental awareness encompasses all key aspects of operational environmental protection, such as waste management, water use, air pollution control and energy saving. The company’s own solar power production contributes significantly to covering its energy needs.
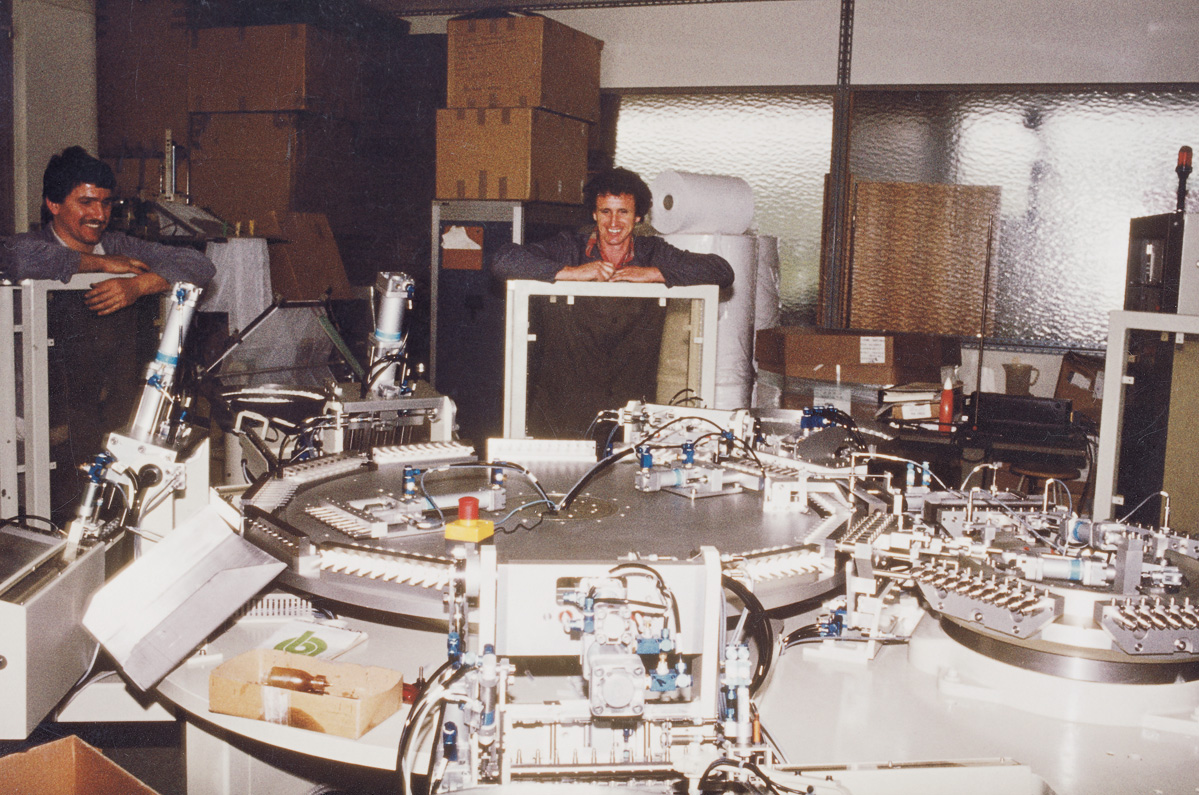
Company history
Family business since 1956
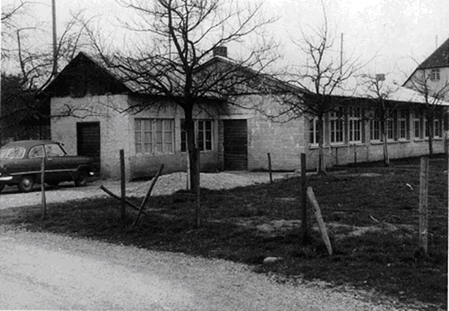